Working for an airline might seem prestigious to most on the outside: a job filled with adventure and travel, with good perks. However, like with most things, reality if very different. For the past nine years, I have spent my time working as an FAA-certified and licensed Airframe and Powerplant Mechanic, or A&P. A&Ps are the lifeblood of civil aviation in the United States.
In short, we are tasked with ensuring that all aircraft in the US are maintained in an airworthy and safe manor. It is not very glamorous, but it sure is fun! I obtained my A&P license by attending an FAA-approved course for two years at a Washington state community college, and then I entered the aviation workforce with gusto and drive, ready to conquer the world; or so I thought!
Throughout my ten years in the aviation industry so far, I have worked for four companies; two for a year or less, and the other two for four years each. I have had the opportunity to work on everything from the diminutive (yet mighty!) Piper J-3 Cub up to the newest member of the 747 family, the 747-8. So sit back and enjoy reading this while I recall some of the adventures (or misadventures!) I have had over the past several years!
According to a popular saying among aircraft mechanics, God made A&Ps so that pilots can have heroes too. Well, I can attest that that is very true! In my four years working for a leading regional airline at Seattle/Tacoma International Airport (SeaTac for short; KSEA), there were many days were I would get called out to a plane that just pulled into the gate with a quick turnaround and the pilot needed something fixed quickly.
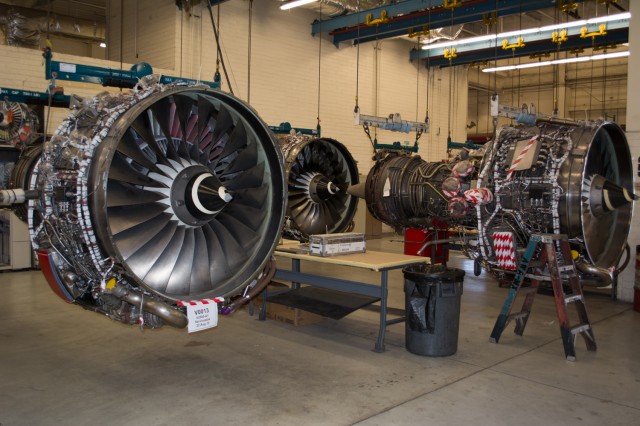
Engines that will one day be back flying the skies – Photo: Jason Rabinowitz
Most of the time, we could do things, such as change light bulbs, quickly. Other times, we would have to spend several hours troubleshooting an issue to find a fix. One particular time, I got called out to a DeHavilland Q400 when the pilot wrote up a tripped deice control circuit breaker. After spending probably four hours checking everything associated with the deice system, consulting the manuals, and talking with coworkers, we had our Ah Ha! moment: we noticed on our wiring diagrams that a wire left the back of that breaker and traveled all the way out to a bleed air control valve on one of the engines.
So I grabbed a ladder, climbed up top of the engine nacelle and checked the connectors on that valve. Sure enough, we had a shorted wire inside the valve. Less than 40 minutes later, after changing the valve and running the engine to check it, we had the plane back in the air and headed to its next destination.
We had a saying at the airline I worked for: If all the mechanics were sitting in the ready room playing cards, reading, or catching up on training, it was a good day. The airline was making money. If any time one walked into the room and found it empty or manuals strewn about, it was a bad day, and we were not making money.
The logic behind that was that if we were all inside, all of our planes were flying smoothly and were out making money for the airline. However, if we were all out working on planes, or inside pouring through manuals, things were broke, and we had planes sitting on the ramp not making any money.
One day, a coworker called me out to a plane to help him pull an engine cowl off a Q400 engine so he could change out an actuator on the cowl. Well, after looking at what was required, and realizing that it would take nearly two hours to fix it that way, we called a third coworker out who was five foot nothing tall, and weighed maybe 100 pounds soaking wet. We had him shimmy on up through the engine intake on the turboprop and change the actuator that way. A simple task — we had the plane back in the air 30 minutes later!
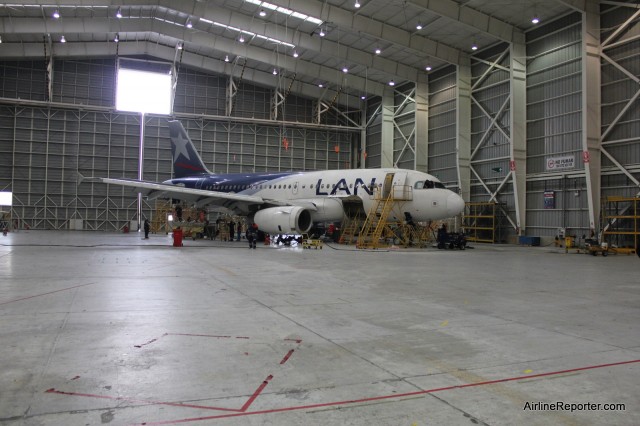
A LAN Airbus A318 being worked on – Photo: David Parker Brown
Another thing that never got old, and I loved, was traveling to fix planes. I would almost never turn down a road trip; however, we all got very good at asking what we would be walking into on the other end.
Sometimes, management would tell us ’œDon’t worry, it’s easy,’ and we would get to our destination to find that everything had gone to hell in a handbasket.
One evening, a coworker and I were sent to Bozeman, MT (KBZN) to repair a Q400 that had to return to BZN after departure when the left engine shutdown in flight. We get into Bozeman at 11:00PM at night, and set to work changing the required parts on the engine, only to find out that we had the wrong part. After a quick call to our maintenance control office in Portland, OR, we had the right parts being dispatched to us by a chartered plane.
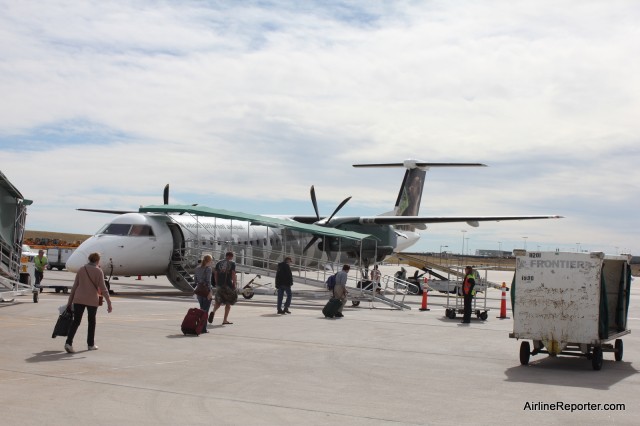
Q400s are great planes, when they are working – Photo: David Parker Brown
So what were two bored mechanics and a customer service manager to do for four hours in the middle of the night? Played poker, of course! After the correct parts came in, it only took twenty minutes for us to change them out, then the fun part of the job: Full-power engine runs! I think we must have woken up the entire town of Bozeman by running both engines at full power for fifteen minutes at 5AM!
Other trips weren’t as eventful: I was asked to go to Santa Rosa, CA (KSTS) one afternoon to fix a hydraulic leak on a Q400. After a 90-minute flight out of SEA in the small jump seat of a Q400 flightdeck (another perk of being a mechanic), I stepped off the plane in California only to be told by the local contract mechanic that he had already fixed the leak.
The only thing I had to do was a quick five-minute ground run of the engine to verify it was fixed. After signing off the log book, and calling maintenance control, I was getting ready to head to the crew hotel when I received a call back from control: they wanted me to fly with the plane on a re-positioning flight to Reno just in case it broke again.
So I met up with the flight crew, loaded up and headed for the Biggest Small City. Of course, the plane did not break again, but I got a free overnight trip to Reno, and only lost $5 at the casino!
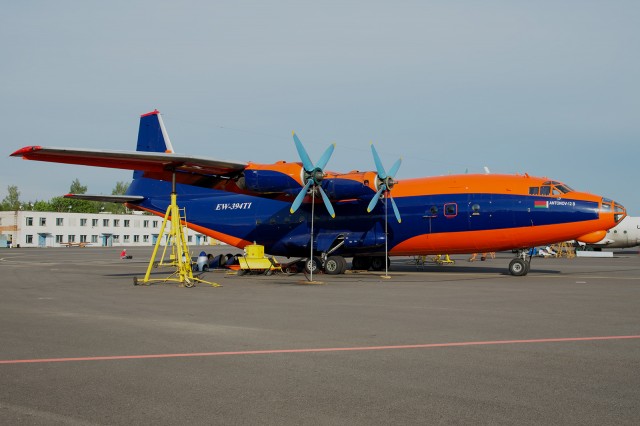
An AN-12 undergoing a maintenance procedure – outdoors – in Mogilev, Belarus – Photo: Bernie Leighton | AirlineReporter
One of the best, and worst, parts of being a mechanic for an airline are the passengers. Many times, I would be called out to a fully-boarded plane for an issue the pilots would have, and find out it is something that would not be an easy fix. I always hated having to tell the pilots to deplane the passengers.
Of course, I would always try to get off the plane and out of sight quickly, because those passengers would be glaring at you for causing their delay. However, some of the best times would be when I, and my coworkers, would be out there busting our butts to get a plane fixed, and be in full view of the terminal windows, with kids and adults alike watching us fix their plane.
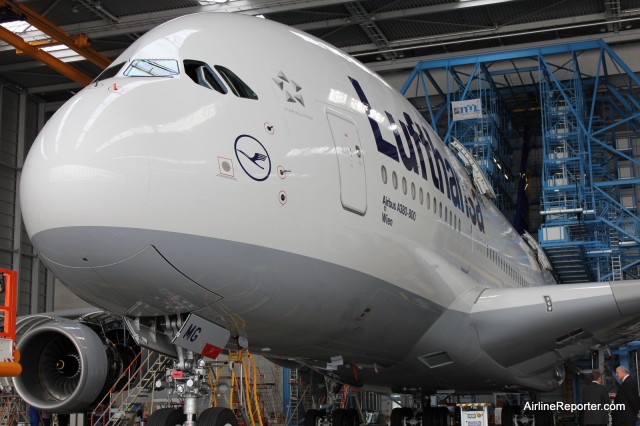
A Lufthansa Airbus A380 gets work done in Frankfurt – Photo: David Parker Brown
It always made us feel better when boarding passengers would thank us for getting them on their way. Nothing was better than that.
A prime example of this was one memorable trip on Christmas Eve. I was sent to Bozeman to fix a broken pilot seat, and after thirty minutes of work, I had the plane up and ready to go. While I stood in the forward galley and filled out the required paperwork, the crew started boarding the passengers. It was a full flight, but I think that all 76 passengers thanked me for fixing the plane and getting them to Seattle that night.
Of course, working around live, operating aircraft can be hazardous. I have seen people nearly walk into spinning prop blades, get blown over by jet blast, or various other close calls. The closest call I had was when I was refilling a portable oxygen bottle for a CRJ-700.
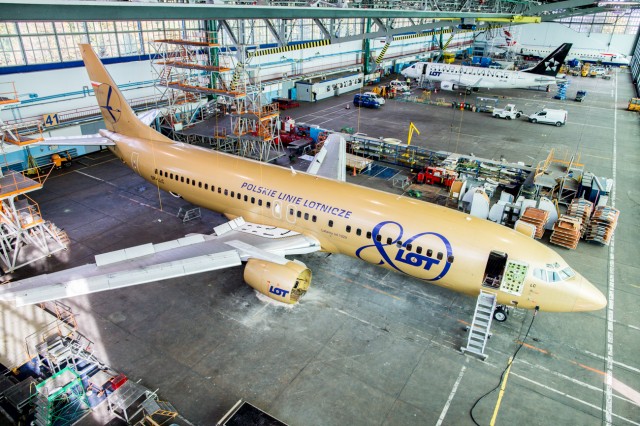
LOT aircraft get worked on in Warsaw – Photo: Jeremy Dwyer-Lindgren
As I was working in a maintenance van next to the plane, the flow regulator on the main master bottle suddenly exploded only two feet from my head. All I remember is a bright greenish white flash, then coming to my senses outside the van sitting on the ground. I was lucky to escape with no injuries, and only a minor concussion from the blast.
Other friends and coworkers have not been so lucky. I have known people who have been run over by landing gear, crushed in spoilers, or even been hit by ground vehicles. It is a hazard of the job, but we all need to maintain situational awareness.
Comments are closed here.
Thanks for this – what interesting stories you must have! The Christmas Eve story must have been the most rewarding part of your job. I hope you write again and share more!
You hit the nail right on the head, I could not have said it better. We worked in different aviation worlds but the stories were the same. The feelings were the same. I did 37 years with a major commercial Airline in Canada from DC8 to DC 10 from 707 ,727,737,747,767 to A310 A320 of course as they aged they were replaced by newer series -100-200-300-400 etc. Everyday was a learning experience. Everyday was a mystery of problems, fixes and camaraderie. We were all special guys doing very important life saving work. I retired 11 years ago and find I still can’t do a half ass job.Everything has to be perfect, and triple checked before I am content. This is hard on those around me but I don’t know how to stop. Maybe I don’t want to stop. There was no room for error on those aircraft. People and in many case even yourself had to rely and trust in you profession and the job you just did to get the aircraft back in the air.
Tiny little unknown hero’s with good pay ,lousy hours ,bad working conditions (in the winter), but great benefits which I still use to this day as often as possible.You young AME ‘s keep at it , enjoy it, live it, love it, and it will give you stories to be proud of to tell the grand kids.
Cheers to all the Aircraft Mechanics Worldwide, I salute you and many more salut you as well silently !! Wrench on !!
A skilled mechanic is a skilled mechanic. Period. The men and women with the A&P certificate are the professionals, the ones who always do it right the first time. My salutes!
I recall accepting a Road Trip to Islip NY. Working for Allegheny Airlines to change an engine on a Convair 440. After 30 hours on the job we were finishing up as the ferry crew arrived to take the aircraft to EWR and be put back in service. The crew asked as to when we would be done. I revealed that we need to do the run-up and run an engine profile to complete the paperwork. It would take at least one hour. The first officer {PIC} said “No Good” ” “I gotta make a “dead head” flight out of EWR to make it home in Pittsburgh, for a diner engagement.” “Can we do the run-up in the air en route to EWR?. Engine #2 started normal, with an ideal BMEP Mag drop and take-off RPM at 2750, and the next thing I know we are rolling down the run-way and quickly rotating. I was in the jump seat with full access to throttle and mixture perform each checklist item, which should have been accomplished on the ground. I read from the check list at loud, while adjusting throttle. The I read “arm auto feather and reduce throttle” which automatically shut down the new engine, as it should. I look, out the cockpit window and realized we were right over the Empire State building, flying “fat, dumb and happy” on one engine. I pull the Feather Button back out counted 3 blades and brought hit the prime button, and the engine started, I brought the mixture to rich and the engine ran better that it should, well it was a new engine. The captain hit the blocks and made the first turn off and made the gate while I folded the jump seat and sat in the back the crew rolled down the stairs, and departed to make the “Dead Head”. Soon the FAA were on the aircraft requesting to see the Log and engine profile. I have told no one of this until now 45 years later, wphew! My check was $900 in 1967.
Hi I like your story it reminds me my road trips locally here in The Philippines and as well ungrounding aircraft abroad as an emergency flight crew. I remember my first AOG in Kansai International Airport, I was only 25 that time. After fixing the A330-300 overnight the best reward was passengers and cabin crew giving you an applause for making the plane airworthy again. Well of course the bonus part was relaxing in the business class. And another one was ungrounding a plane when there was an approaching typhoon. My colleague and I was given 4hrs due to approaching typhoon and make the plane airworthy again. We finished our work half of the given time and hand an engine run up for 30mins to for vibration survey and fly. That was a bumpy ride. Overall being an aircraft mechanic is one of the most adventurous job and I will always love my job as an aircraft mechanic tiring yet rewarding.
One thing I liked about the article is that you have to be very careful when it comes to this kind of repair gear, you have to be careful with using it since it’s a delicate piece of equipment that has to support the weight of an entire airplane when it’s being used for repair. At the same time, it’s also a good idea to be very careful when going around a plane for repairs, because safety is always first! While I have no experience with flying a plane, at least the similarities of having to be careful around live aircraft are just like being careful when driving a car: you have to be careful!