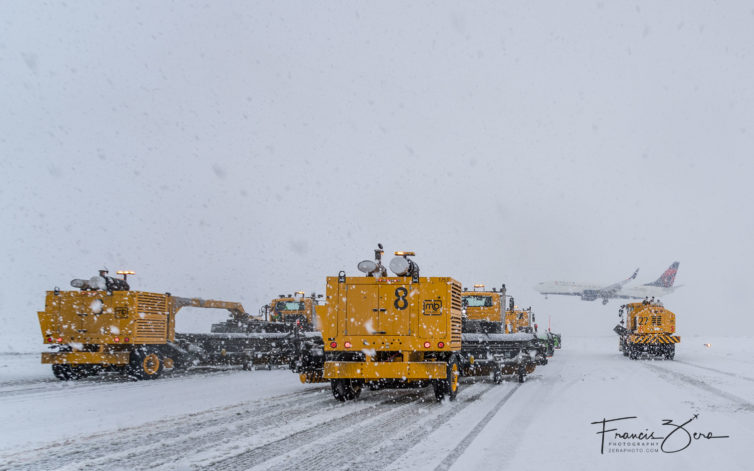
The Seattle area has seen unusually heavy snowfall over the past week – 20.2 official inches of snow over six days. The heavy precipitation has closed local roads and freeways, caused widespread power outages, and generally raised havoc in an area that doesn’t normally receive noteworthy levels of snow. This is the most snowfall seen in Seattle for the month of February since 1916, and we are just half way through the month.
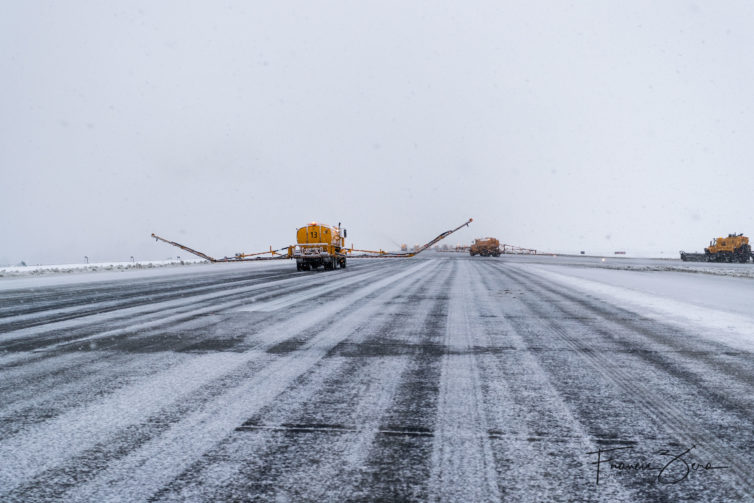
Seattle-Tacoma International Airport’s (SEA) ever-increasing flight volumes leave little room for weather delays. To contrast with the City of Seattle, which keeps just 35 snow plows on hand for the entire city, Sea-Tac Airport has more than 45 pieces of major snow-removal equipment, including:
- Nine plow and broom combination units – state-of-the-art trucks with a 24-foot plow that’s as long as a semitruck
- Two friction testers to measure stopping distance for the runways
- Three sander/plows
- Seven high-speed plows
- Four de-icing trucks for roadways (three 75’ wide booms, one 45’ boom)
- Additional sand, plow, and chemical trucks dedicated for landside maintenance
- Pickup trucks with sanders and plows
- Five snow blowers
- 10 high-speed brooms
- Walk-behind snow blowers
- Lots of snow shovels and brooms and team members ready to work
This week I was able to ride along with airport operations and see what it takes to keep operations at the airport moving.

Airside, it takes about 45 minutes for a team of vehicles to clear one of the airport’s three runways, which is, of course, closed to air traffic while the crews at work.
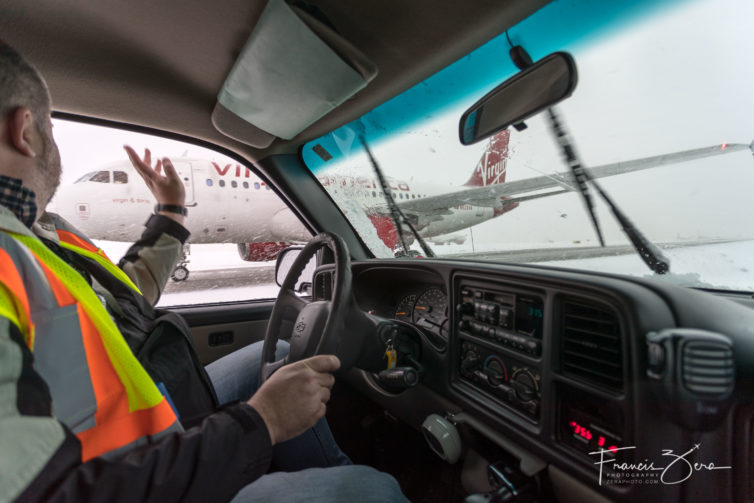
In times like these, operations teams pull together. For example, Joshua Marcy, Sea-Tac’s manager of terminal operations, also has extensive airside experience, so he went out to help with snow removal.
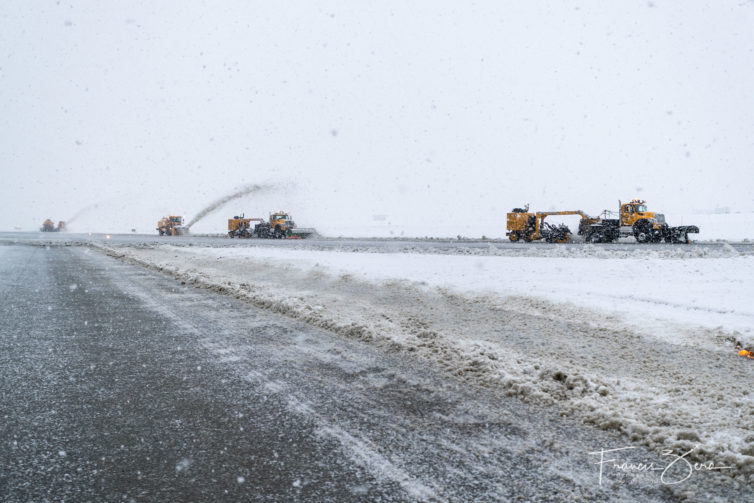
The airport has crews that are responsible for snow and ice removal on runways, taxiways, and all ramp areas. In addition, the airport has other crews that work diligently to clear and maintain the terminal area, parking garage (Sea-Tac boasts the second-largest parking structure on the planet, so that’s no small feat), several surrounding roads, and the multi-lane entry drive leading to the terminal from the freeway.
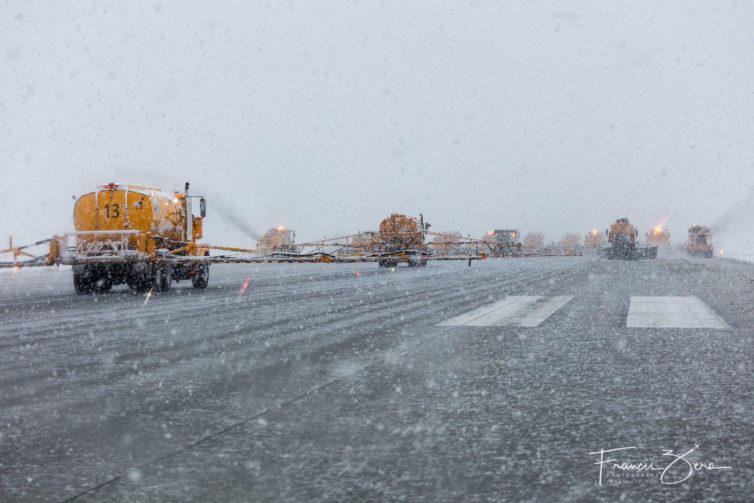
Airlines are responsible for de-icing aircraft, and Seattle-Tacoma International Airport Senior Manager of Media Relations Perry Cooper said that each airline has their own staff or contractor that they work with. “Some of the smaller airlines, such as the infrequent internationals with only one flight a day, will work with the same group, like Swissport, to do their de-icing. I did speak with one of our people with the airline consortium and they estimated there are probably about 50 or more de-icing trucks throughout the airport among the airlines,” he said.
-
Some aircraft are de-iced at the gate -
Others are done at remote stands -
Not all de-icing rigs have enclosed cabs
The large V-formation of snow removal vehicles we got to see was a combination of two crews working together in order to clear the runway in one pass. Cooper explained that “this was necessary due to the volume of snow at the time. Normally, they would have one of those teams do two passes to clear the entire runway. This consists of four combo plow/brush rigs, followed by a rotary that shoots the snow to the side, another single broom, a sander, and then a de-icing truck. So the V had two sets of that group in total.”
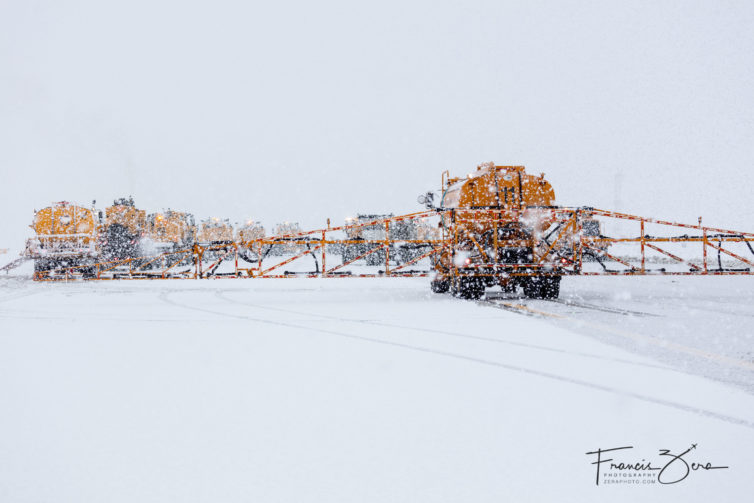
Riding along in a pickup behind the huge plows and other equipment as we all drove along a runway at an international airport was an amazing experience. We had the windows open so I could take better photos, and large snowflakes swirled around inside the truck as we sped along. It was interesting how quiet it all was, though – the snow really mutes sound.

Sea-Tac’s runways have embedded temperature monitors that allow staff to know to apply anti-icing fluid only when necessary in order to conserve the supply. On-site tanks store 62,000 gallons of anti-icing fluid.
Cooper shared the amounts of de-icing products the airport has used so far this year:
- 75,000 gallons of runway deicer
- 63 tons of solid runway deicer
- 250 tons of AOA sand (specific sand regulated for the Airport Operations Area. Per Cooper, “it’s not just sand you find in Lowe’s or what’s used on a street. It’s a regulated size that won’t damage items you find on an airport like aircraft engines.”
“This is about twice what we typically use, and we’ve spent about $1 million in purchases just this month, when we have averaged spending about $500K for the year over the past five years,” he said.
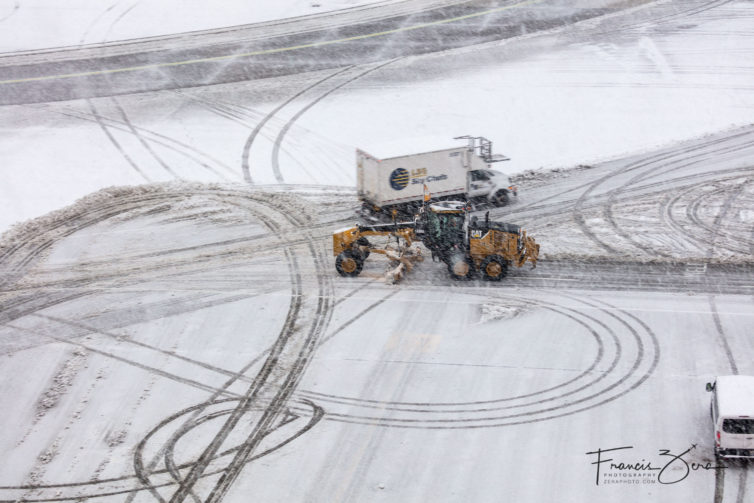
Snow removal on runways takes a huge amount of coordination between the drivers of the vehicles themselves, air traffic control, ground traffic control, the lead car in the convoy, and the sweep car. Then there are all the ramps to clear and coordinate with ground controllers, and then the landside areas. It’s a city unto itself.

So, the next time I’m flying on a snowy day and my flight is a bit delayed, I’ll likely be lots more patient now that I have a better understanding of just how much work goes into keeping an airport open in inclement weather.
Thanks Francis for a unique, fascinating and well-written article. These stories are what makes Airline Reporter so great.
Thanks for going out there in the cold to get these photos.
Hi Drew, Thanks for your kind comment!
Thanks, Harriet. It wasn’t all that cold, truth be told. And l love the snow.