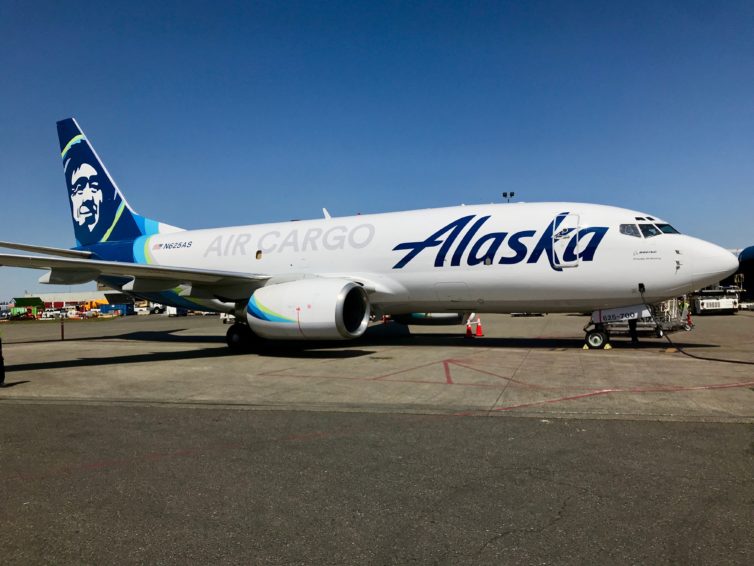
One of Alaska Airlines three newly-converted 737-700 freighters on the ramp at Seattle-Tacoma International Airport
Ever wonder about the process of loading, unloading, organizing, tracking, and planning the cargo side of a cargo flight?
Wonder no more Alaska Airlines recently invited us to watch (and then ask a metric ton of questions about) one of the airline’s new 737-700 freighters on a recent visit to Seattle-Tacoma International Airport.
“Alaska Air Cargo serves as a lifeline to many of the communities in Alaska where we fly,” said Jason Berry, managing director of cargo for Alaska Airlines.
“Offering reliable and consistent service is critical for us. The addition of our modern fleet paired with our proprietary navigation procedures allows us the ability to bring true scheduled service to the far north,” he said.
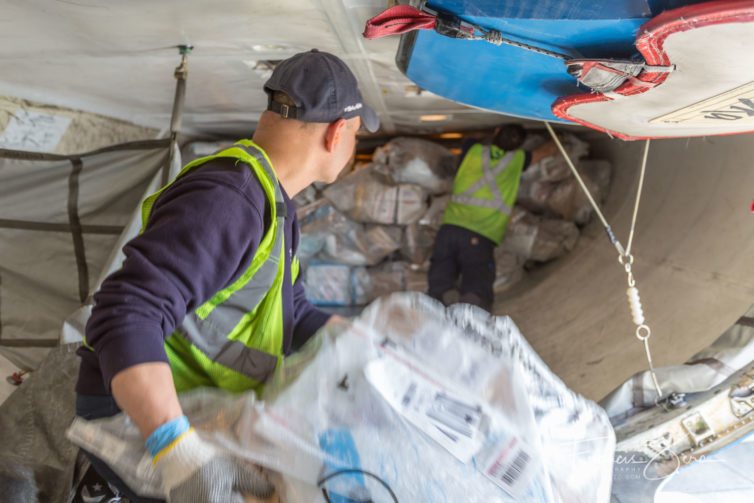
Alaska Airlines Ramp Service Agent (RSA) Carlos Arenas, foreground, prepares to pass a bag of mail to Lead RSA Metin Mehmedov. Both are working in the aft belly hold of the aircraft.
In preparation for the induction of Alaska’s first Boeing 737 MAX aircraft, the company’s strategy was to retire the remaining 400-series ’œclassics’ from its fleet. The five combis and single dedicated freighter were all 400-series aircraft.
According to Berry, those 400s were also getting extremely cycle-heavy, which meant they had so many takeoff/landing cycles that they were nearing the end of their useful life for Alaska Airlines.
“The decision to convert three 737-700 Next-Gen passenger aircraft to freighters meant we retain much of the same fleet commonality in terms of training and maintenance and it would give us the right-sized aircraft to still serve all the same communities we provide main deck cargo lift to today (-800s could not land at some of our current scheduled airports such as Adak, Kodiak, Petersburg, and Wrangell),” he explained.
And what’s become of those old cargo planes? Berry said all six were sold to leasing companies. “I believe you can find them for sale as we speak. I speculate that someone will eventually purchase the aircraft and convert them to full freighters.”
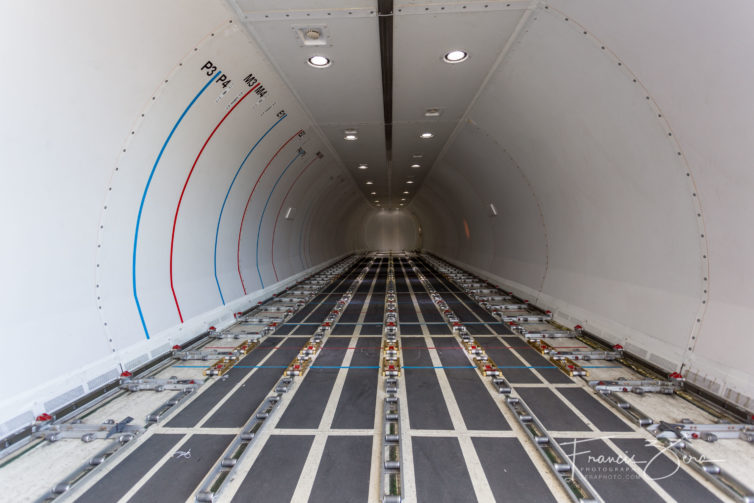
The soon-to-be-filled cargo hold of one of Alaska Airlines’ new 737-700 freighters
OK, now for the fun, nerdy stuff. Berry said that the new freighters can carry approximately 39,500 lb. at maximum load under optimal conditions. Compare that with the old combi aircraft, which were extremely weight sensitive and dependent on having the right number of passengers booked in the rear compartment. “We would normally move 12-13,000 lb. per flight. The previous freighter could carry approximately 36,000 lb.,” he said, so the new freighters have a cargo-carrying advantage of 3,500 lb. over the old freighter and a whopping 26,500 lb. capacity increase over the combis, although the dedicated freighters can’t, of course, carry any passengers.
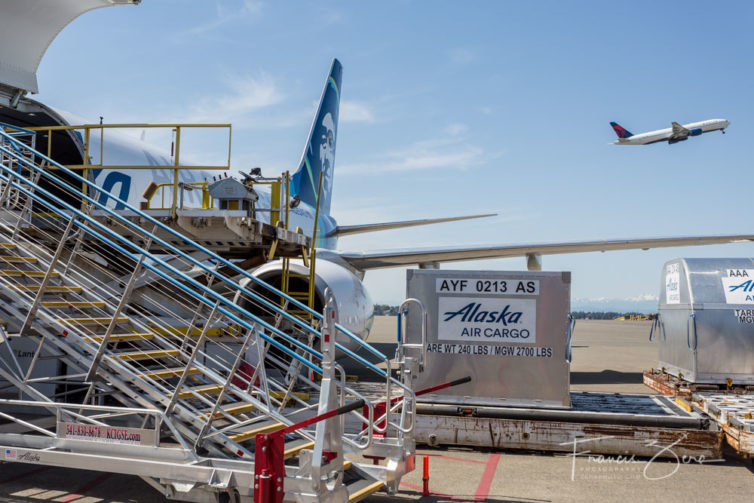
Cargo ramps are busy places
Alaska Air’s three 737-700 freighter conversions are the first of their kind. “Since taking delivery of our last aircraft at the end of February, we’ve quickly ramped up our scheduled service, flying our aircraft 10.5 hours per day averaging 6.7 daily cycles this is a considerable metric for a narrow body aircraft,” Berry explained. “You would be hard pressed to find any other similar freighter operators of similar sized narrow body aircraft achieve these types of results. We are putting similar demands on our freighter schedule as we do on our passenger side. This is a testament to our amazing ground crews, pilots, and maintenance and engineering teams.”
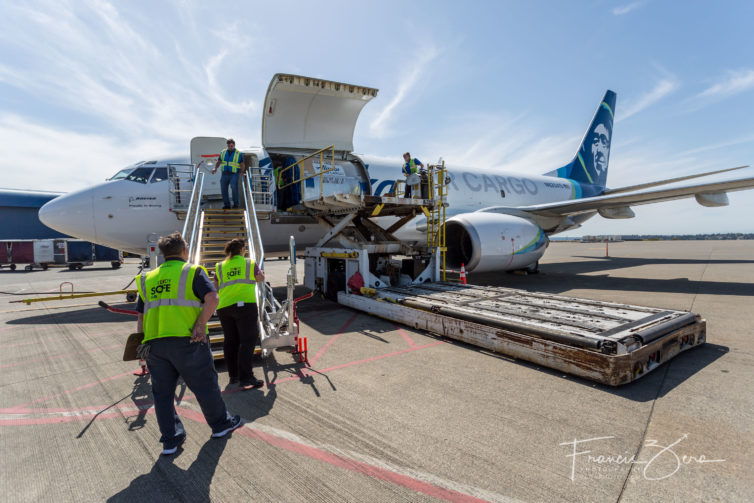
Loading cans via the big cargo door on a 737-700 freighter
Berry explained the process of a cargo turn, starting from the beginning. “The process begins with pre-planning. This includes reviewing what is booked for the flight and what is currently available and on the floor. From there, our ramp team will begin build-up of the 10 ULD (a unit load device, aka pallet, container, or ‘can’) load, working to maximize the loads,” he said.
The flight that we photographed in late April was flying SEA-KTN-SIT-JNU-SEA (Seattle-Ketchikan-Sitka-Juneau-Seattle), which meant the cargo team had to prepare the flight to best support each of the stops along the way, paying attention to details such as making sure to build ULDs so they can be loaded with the JNU cargo in the back to prevent KTN or SIT from having to unload anything more than is necessary, thereby saving time.
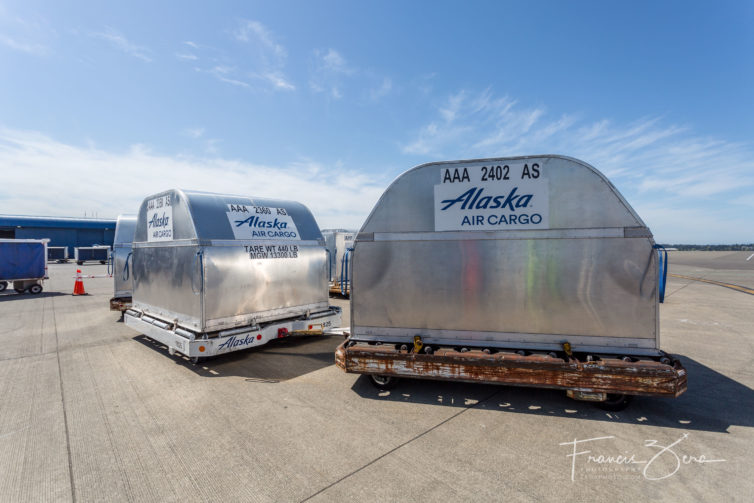
Filled cans on the Seattle cargo ramp, ready to be flown to Alaska
Berry continued: “Once our ULDs are built, the cargo manifest is electronically submitted to our Central Load Planning team (CLP). This group uses our weight-and-balance program to achieve the best possible center of gravity, while also considering the most efficient load for the downline station.
“Once the load plan is completed it is electronically published and sent back to the cargo warehouse and includes loading instructions (details of any special handling requirements, notification of where any dangerous goods are located, live animals, etc).”
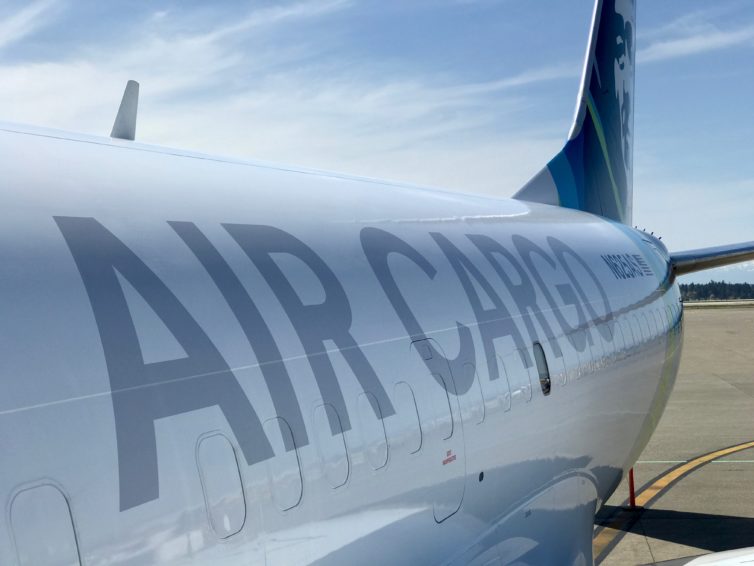
Alaska Airlines flies their cargo jets nearly as much as their passenger aircraft, which is unusual in the industry
On the day we visited, the aircraft had a 50-minute scheduled turn time, as it was arriving from KTN (Routing was ANC-JNU-SIT-KTN-SEA). Prior to arrival, the crew prepared the ramp, performing a FOD (foreign object debris) walk and a safety check of the area, then organizing their pallets/containers to most efficiently offload the inbound load and organize their outbound containers into strings that make the process move as smoothly as possible.
One on the ramp, the aircraft’s wheels are chocked and it is immediately offloaded, so the inbound cargo can be brought into the warehouse and promptly checked in. “Approximately 60 percent of all cargo that touches our SEA facility is transit cargo, meaning it is arriving off an aircraft or connecting once it gets here,” Berry said, adding that the warehouse teams will break down the ULDs in order of priority, processing those that have connecting cargo first.
An average turn consists of six ramp agents, including a ramp lead and a departure coordinator. Cargo supervisors attend many of the turns as well to serve as a link to the different work groups should any issues come up, such as a need for additional fuel, changes to the catering for the crew, etc.
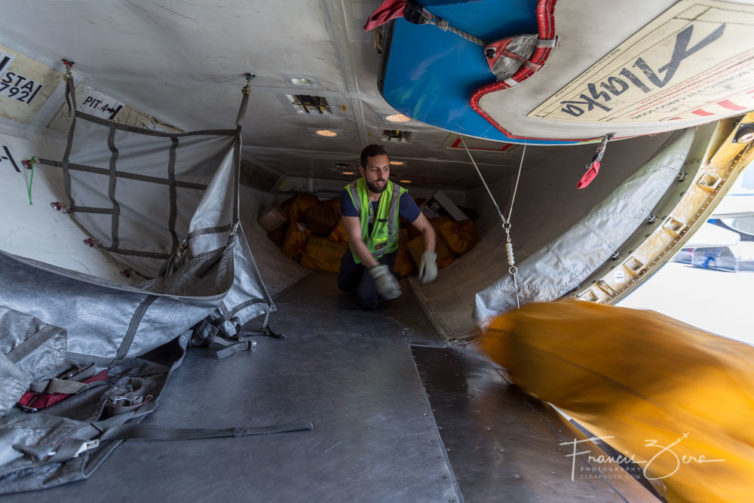
Lead RSA Metin Mehmedov unloads bags of mail from the inbound flight
Once the offload is completed, the team reviews the outbound load sheet again to confirm the loading order of the ULDs, and upload begins. “On the main deck of the aircraft, the team lead scans the bar code of each ULD, and then scans the bar code on the side wall of the aircraft located in the position that we are locking the ULD into. This is a positive-match scanning process to ensure all of the ULDs are loaded in the correct sequence and locked in the right position” for both proper efficiency and for proper weight-and-balance calculations, he said.
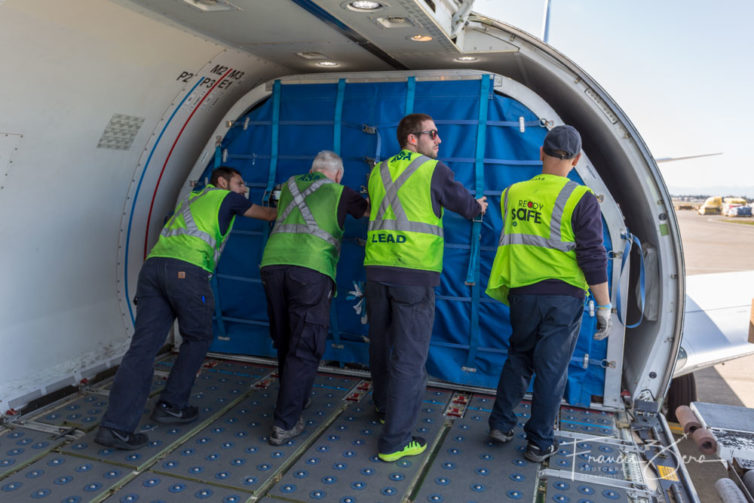
Once on board, each pallet is pushed into place by hand – the cargo-hold floor is covered with small bearing-like wheels
All 10 cargo positions in the plane’s upper hold are then loaded and scanned. Any ULD/location that does not match the original plan will signal an error on the hand-held scanner that will require the loading team to stop and resolve before moving forward or dispatching the aircraft. “This is a great safety protocol we have built into our aircraft to preserve load integrity,” Berry said.
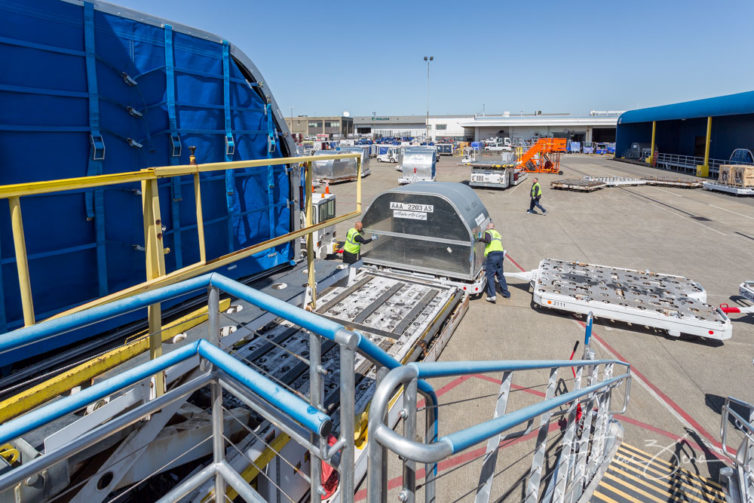
The loading process is very efficient – it seems to take no time at all to load or unload the containerized cargo pallets from the upper deck
After all the cargo is loaded into the belly holds and main deck, the departure coordinator (DC) will confirm that all the ULD scans match, he or she then calls in to confirm the load with the central load planning (CLP) team. Once the load has been confirmed, the flight is released and readied for dispatch. The ground crew in SEA then prepares for pushback and sends the aircraft on its way.
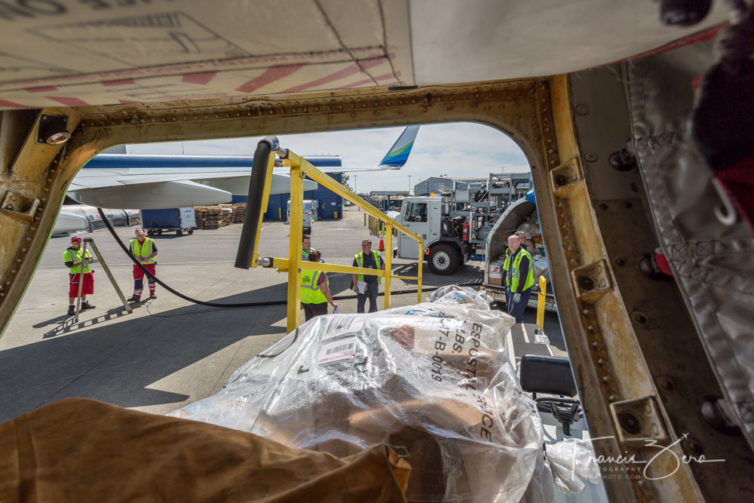
Bags of mail are loaded into the aft belly hold
Berry said their primary commodities carried are perishables (seafood, produce, meat, etc.), e-commerce deliveries, mail, live animals, pharmaceuticals, and other products requiring time-sensitive/express service.
“We are proud of the small role we play in Alaska to keep commerce moving safely and on time. Our company was founded over 85 years ago, carrying mail in the great state of Alaska, and our freighters help us carry on this tradition,” Berry said.
Great article!
Thanks, Mike! It was really fun to learn about, too.
GREAT article. I work for UPS Airlines here in Louisville, KY (ACMX Technical Publications (wiring diagrams, schematics for our B757s and B767s.) We can definite relate to everything mentioned. Been there – continuing to do all that!
Thanks for reading, RayLRiv, and it sounds like you have a cool job, too!
Can any AS pilot fly the freighters, or does AS Cargo have its own pilots?
Hi James,
That’s a great question, and thanks for reading .
I just emailed Jason Berry, who is the managing director at Alaska Airlines Cargo.
Here”s what he said:
”All AS pilots can fly the freighters. We do not have our own crews. Both our maintenance and flight crews come from mainline support.”
So there you have it – any Alaska Airlines pilot can fly the freighters.
Appreciate you reaching out to Jason for that answer! That’s good to know.
Thanks again – James
Happy to do it, James. It was a great question and I was curious about the answer myself.
That was a great question – James. Thank you. And thanks to Francis for the good article, great pictures, and fast followup. Thanks for telling the story of why 700’s were converted instead of larger planes.
My question…..I see the belly cargo is loose loaded just like the bags on a passenger flight. I assume both holds are used the same way. Since the doors swing in, is there a chance that cargo can shift in flight and make it difficult to open the door? Or is everything by the door tarpped and strapped?
Hi Chris,
Thanks for reading!
To answer your question, the belly hold is loaded just like on passenger flights, yes. The cargo is held in place with netting and straps that don’t allow it to shift in flight.
You can see that netting on the left side of the eighth photo (counting from the top) of the article. It has the caption of “Lead RSA Metin Mehmedov unloads bags of mail from the inbound flight.”