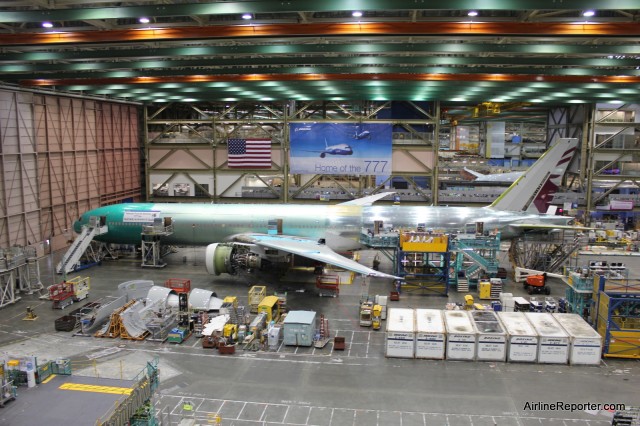
Taken in February 2011 inside the Boeing Factory, this 777-300ER is the 24th 777 for Qatar.
So how long does it take Boeing to build a 777? That was a question emailed to me by reader Ron Thomas and I realized I did not know. I posed the question to Boeing on how long it takes for a 777 to be built and out of the factory, how long it takes to be painted and then how much longer before actually being delivered to a customer. I decided to share the answers.
Of course depending on the paint job and possible issues, these numbers can change, but this is based on the average build for a 777:
From first part to out of the Boeing factory in Everett: 49 days
Time in the paint booth: 4 additional days
Flights and testing: About 30 additional days
Total from first part to delivery: About 83 days — less than three months.
That truly is beyond impressive and if you have ever taken a tour of the Boeing factory, you know that they make it look so easy.
Over the past week I have been receiving many different press releases from Boeing – most of which I wanted to share, but haven’t had the time to give them the attention that they deserve. To make sure that they all get a little attention, I decided to do this round up to touch base on what’s going on with Boeing. There are a few more story lines that I hope to go into a bit more detail over the next few days, but for now…
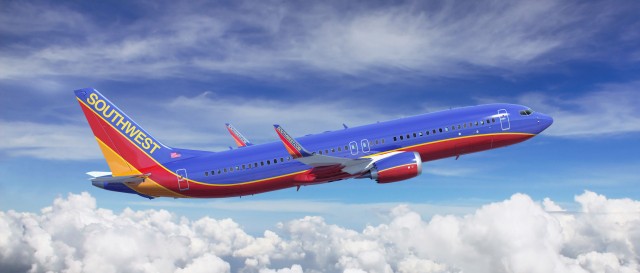
HI RES (click for bigger): Southwest Airlines Boeing 737 MAX 8. Photo by Boeing.
SOUTHWEST AIRLINES BECOMES LAUNCH CUSTOMER FOR THE 737 MAX
On December 13th, Boeing announced that Southwest airlines placed an order for 150 of the 737 MAX and would become the launch customer the new version of the 737.
“Southwest is a special Boeing customer and has been a true partner in the evolution of the 737,” said Boeing Commercial Airplanes President and CEO Jim Albaugh. “Throughout our 40-year relationship, our two companies have collaborated to launch the 737-300, 737-500 and the Next-Generation 737-700 ’“ affirming the 737 as the world’s preferred single-aisle airplane. As launch customer for the 737 MAX, Southwest, Boeing and the 737 continue that legacy.”
The firm order is Boeing’s largest in both dollar value and the number of aircraft ordered.
“Today’s environment demands that we become more fuel efficient and environmentally friendly, and as the launch Customer of the Boeing 737 MAX, we have accomplished both,” said Gary Kelly, Southwest Airlines Chairman, President, and CEO. “We are teaming up with our friends from Boeing to lead the industry in a way that makes both our shareholders and our Customers proud to associate with Southwest Airlines. Today’s announcement will allow us to maintain our position as a low-cost provider in the years ahead.”
VIDEO: Southwest Airlines Boeing 737 Max. Computer generated by Boeing. Thanks to Robert for pointing this out.
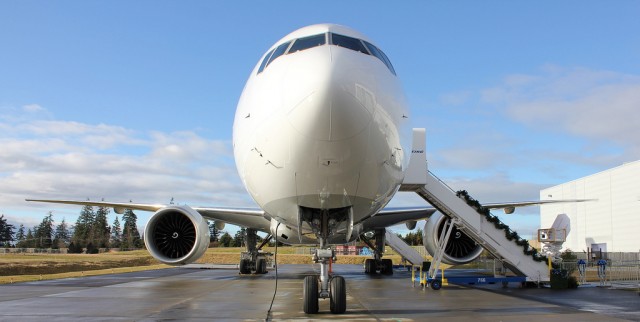
Air New Zealand's first Boeing 777-300ER at Paine Field. Photo by AirlineReporter.com.
BOEING 777 NOW HAS 330-MINUTE ETOPS
On December 12th, Boeing announced that its 777 received approval from the Federal Aviation Administration (FAA) to fly up to 330-minutes away from an alternative airport.
“Boeing twin-engine jets have flown more than 7 million ETOPS flights since 1985, and more than 120 Boeing operators fly more than 50,000 ETOPS flights each month,” said Larry Loftis, vice president and general manager 777 program. “This is the logical continuation of the Boeing philosophy of point-to-point service. Passengers want to minimize their overall travel time. This is one more step in that direction.”
To date, the 777 has flown more than 2 million ETOPS flights since June 1995 and 93% of 777s are flown on ETOPS routes.
“What this means is that the airplane is able to fly a straighter route between the city pairs and that’s good for the environment,” said Capt. David Morgan, chief pilot for Air New Zealand. “Less fuel is burned and less carbon dioxide is emitted into the atmosphere. It’s also good for customers because flights are potentially shorter and passengers could arrive sooner at their destinations.”
CHECKING IN WITH THE DREAMLINER WORLD TOUR
Boeing’s third Dreamliner, ZA003, is taking a six month journey around the world. Its first stop was in Beijing, China with different stops with-in China from December 4th to 11th.
“This great day demonstrates our partnership with China in pursuing aviation excellence,” said Marc Allen, Boeing China president. “Chengfei, Hafei and Shenfei — as exclusive and single-source Boeing suppliers — have made a great contribution to the success of the 787 program, producing the rudder, wing-to-body fairing, and vertical fin leading edge. We want to thank them for their role in making today possible.”
On the 11th, ZA003 flew over to Africa and became the first time a 787 has landed in that continent. From the 11th to the 14th, the 787 hung out in Nairobi and allowed Ethiopian Airline employees the chance to see the new aircraft they should be taking delivery of soon. ZA003 will remain in Africa until the 16th of December before flying to the Middle East with a stop in Doha to visit Qatar Airways.
At this point, Boeing has not announced future destinations, but I would imagine that ZA003 will continue to head west.
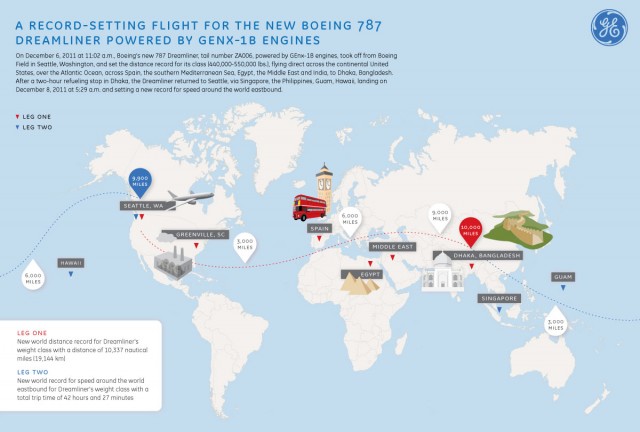
Graphic showing the record breaking Boeing 787 Dreamliner flight. Image is from GE. Click for larger.
THE 787 DREAMLINER BREAKS WORLD RECORDS
While ZA003 is traveling the world, ZA006 went and set some new world records. The 787 Dreamliner recently established two new records for speed and distance for the aircraft’s weight class.
From Boeing’s press release, “The sixth 787, ZA006, powered by General Electric GEnx engines, departed from Boeing Field in Seattle at 11:02 a.m. on Dec. 6 and set the distance record for its class (440,000-550,000 lbs.) with a 10,710 nmi (19,835 km) flight to Dhaka, Bangladesh, with credit for 10,337 nmi (19,144 km). This record had previously been held by the Airbus A330 based on a 9,127 nmi (16,903 km) flight in 2002.”
“Following an approximately two-hour stop for refueling in Dhaka, the airplane returned to Seattle on a 9,734 nmi (18,027 km) flight. The airplane landed at 5:29 a.m. on Dec. 8, setting a new record for speed around the world (eastbound) with a total trip time of 42 hours and 27 minutes. There was no previous around-the-world speed record for this weight class.”
Go Dreamliner go!
OTHER BOEING HEADLINES RECENTLY:
* FedEx announced order for additional 767 and 777 Freighters
* Boeing 747-8 Intercontinental Receives FAA Certification
* Ethihad Airways Orders 10 787-9 Dreamliners
* Boeing to Build New Everett Delivery Center at Paine Field
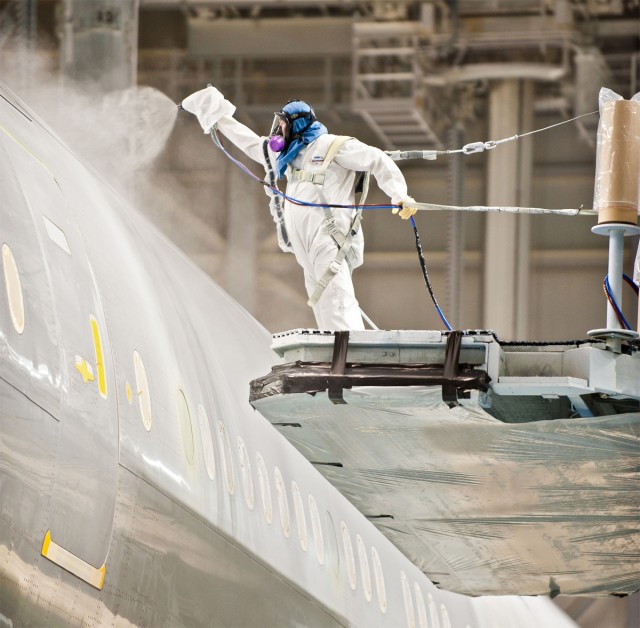
Boeing painter Bill Pearson applies chrome-free primer to the 777-300ER that was delivered to Air New Zealand in November 2011. Photo from Boeing.
Boeing has announced 10 initiatives on the 777 program that will help to eliminate 5.5 million pounds of CO2 and 300,000 gallons of jet fuel per year just in the 777 delivery process.
A lot of attention is given to how airlines can save money and the environment when flying them, but how about aircraft manufactures saving a little green (money and environment) before an aircraft is even delivered?
Before each 777 is delivered, there is a 20-day process of paint, tests and flights before Boeing hands over a brand plane to a customer. Boeing has been working on creating a more efficient process with Air New Zealand, which took delivery of a 777 using all ten initiatives.
“A team of employees identified redundancies in testing,” said Jeff Klemann, vice president Everett Delivery Center stated in a press release. “One idea was to eliminate engine-run tests already performed by GE, the 777’s engine manufacturer. This will result in a reduction of 1.4 million pounds of CO2 in 2012 as well as less community noise and emissions.”
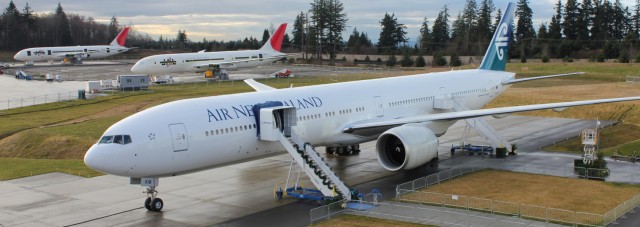
In December 2010, Air New Zealand took delivery of their first Boeing 777-300ER. Photo by AirlineReporter.com.
A team of employees identified redundancies in testing and new more sustainable processes.Through out the 777 delivery process the team implemented the following 10 initiatives:
* Eliminated redundant fuel test in pre-delivery flight test
* Reduced the amount of times hydraulic filters are changed
* Eliminated engine-run tests already performed by GE
* Used waste fuel carts
* Reduced the number of times potable water is changed
* Reduced the amount of times engine fuel filters are changed
* Enhanced recycling throughout the delivery process
* Used electric carts instead of gas-powered vehicles
* Improved flight planning efficiency for pre-delivery flights to reduce fuel loads and flight times
* Used chrome-free primer
Nine of the initiatives will come standard with all future 777 deliveries. Usage of the special chrome-free paint will be an airline option.
MORE AIR NEW ZEALAND 777 STUFF:
* Behind the scenes of an ANZ 777-300ER delivery
* Checking out the interior of ANZ’s 777-300ER
Singapore Airlines gave a special tour to invited media guests to their training facility located in Singapore and I felt privileged to be among the group. We were able to experience the flight attendant safety training, cabin crew procedure training and the flight simulators.
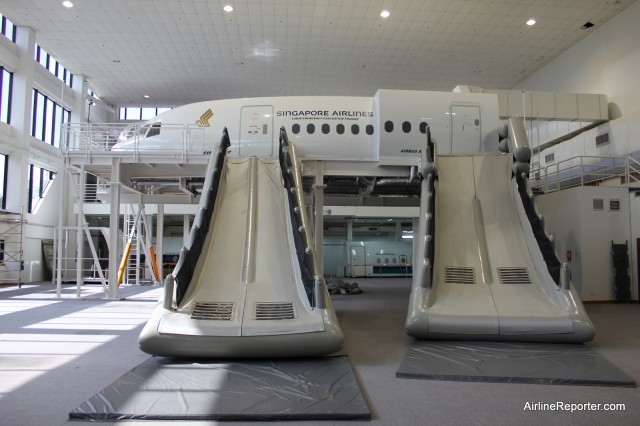
The slides are not for fun. This hybrid of Boeing 777 and Airbus A380 is to teach cabin crew how to evacuate an airplane.
We first entered a large room that looked almost like a play ground with slides, but it was all business. This is where cabin crew learn and get re-trained on safety protocols. There were a number of different interior mock ups and the most interesting was the hybrid slide trainer. This was a unique set up with a Boeing 777 in the front and an Airbus A380 in the rear. The aircraft is used to allow flight attendants to practice evacuating passengers and jumping down the slides themselves. Inside the mock up, the interior was made up of earth-toned seats, with half of it being wider than the other half. The emergency doors had LCD screens located in the windows to simulate what might be on the other side (ie fire, debris) and the flight crew must react accordingly. Other mock ups in the facility allow cabin crew to practice opening emergency doors, escape from crew quarters and learn the proper operations on different aircraft.
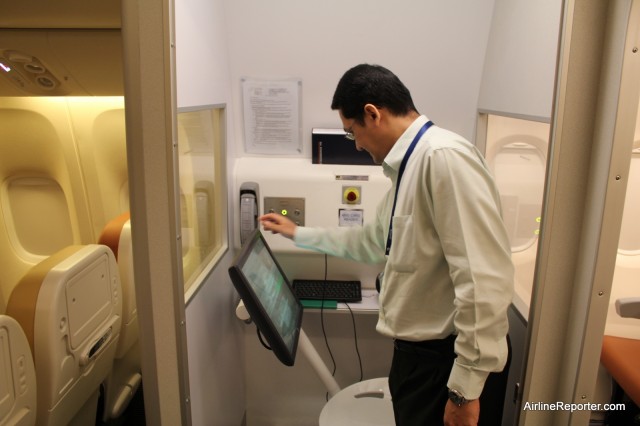
Instructors are able to set up a number of different scenarios for flight attendant training.
The larger hybrid airline cabin is able to be filled with smoke to simulate an emergency situation (see an example from when I visited AirTran). There is a control panel that lets the instructor set up a scenario and the flight attendants must react accordingly. I was hoping to have an opportunity to take a slide down, but decided on the stairs instead.
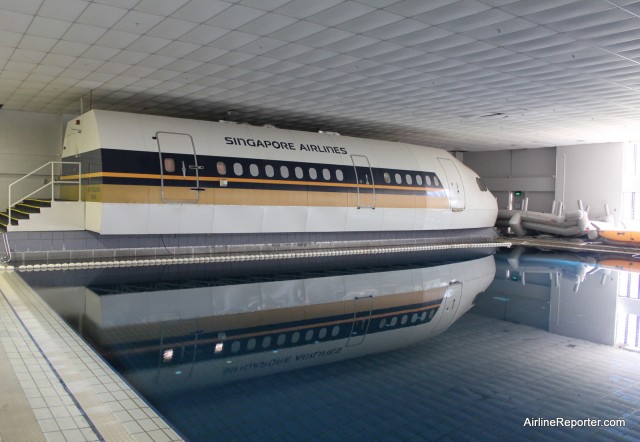
The water is calm in this photo, but during training, instructors can make waves in the Singapore Airlines training pool.
After coming down the stairs, we went into the pool training facility, where flight crew are required to practice jumping into the water with their uniforms. The pool is able to simulate waves and rough conditions, providing an additional challenge for the new trainees. Much like the slide trainer, the interior has a full cabin set up, giving as much realism as possible to an actual water landing event.
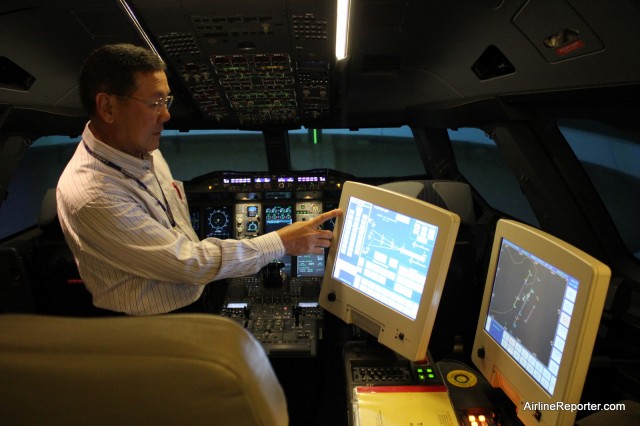
Singapore Airline's Airbus A380 flight simulator has a Star Trek like command chair for the instructor to create almost any scenario possible.
The training facility also operates seven aircraft simulators that cost between $12million and $30million. Singapore Airlines leases time on the simulators for other airlines as well, except the Airbus A380 since they need all the time on it as possible. The A380 simulator is unsurprisingly big and although it is a massive beast — she flies like a champ. The simulators have full motion giving pilots realistic g-forces during landing, take off and maneuvers. Instructors are able to sit in a command seat behind the pilot and co-pilot to create dangerous situations at airports around the globe. Before pilots take a spin on the larger simulator, they are able to practice the proper procedures on a much more simplistic (and cheaper) Flight Training Device.
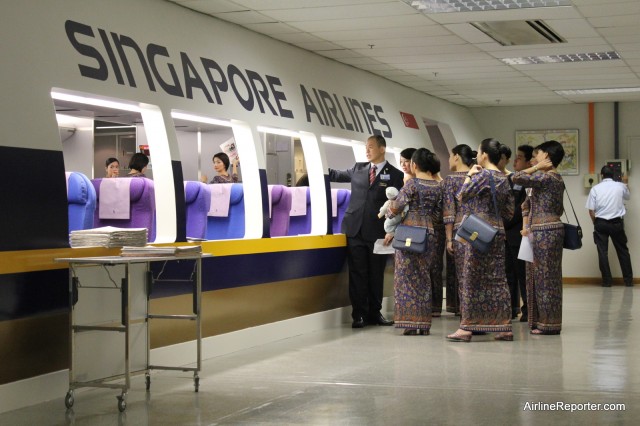
New Singapore Girls learn how to work the economy section at the training facility.
Even though safety is the most important aspect of a flight attendants job, a large portion of the facility is set up to teach flight attendants how to take care of their customers. Down a long hallway, there are multiple mock-ups to let new employees learn customer service for economy, business and first class passengers. Interestingly, part of their training includes greeting facility guests with a warm welcome. It is quite impressive to walk by a group of 25+ new flight attendants and have them all welcome you to the training center.
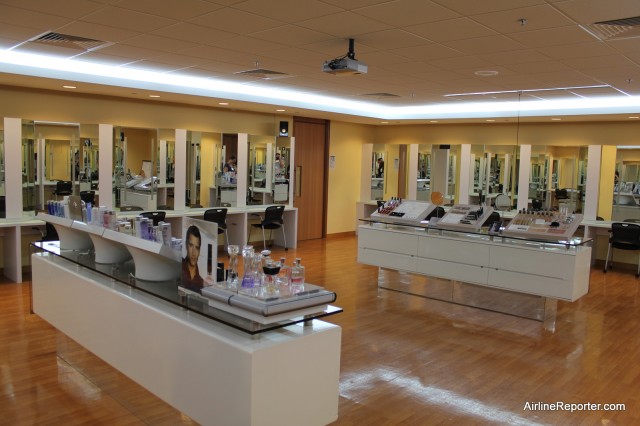
Looks and proper grooming is important to Singapore Airlines. This room, new hires learn how to look professional during long flights in a low-humidity environment.
First impressions are important and Singapore Airlines makes sure their entire flight crew look professional. Even though the male crew won’t be wearing any make-up, they still go through the full training to learn how to keep their skin from getting too dry and how to assist their female co-workers. There is a classroom dedicated to make-up and scents training and another for flight attendants to practice walking properly.
Singapore Airlines is known for their high-end service and it takes quite a bit of work to accomplish. Besides basic training, flight crew are required to return for additional and advanced training. Even though the facility might look like fun and games, everything done there is for either customer service or safety. Both are very important aspects to running a successful airline and it seems to be working quite well for Singapore Airlines.
CHECK OUT ALL 30 PHOTOS OF SINGAPORE AIRLINES TRAINING FACILITY
-
-
From the JFK tarmac: ANA Boeing 777-300ER (JA786A). Manny Gonzalez / NYCAviation
-
-
The updated livery up close. Manny Gonzalez / NYCAviation
-
-
ANA Boeing 777-300ER (JA786A) with updated livery. Manny Gonzalez / NYCAviation
-
-
ANA Boeing 777-300ER (JA786A) with special Japan Relief livery at JFK. Manny Gonzalez / NYCAviation
Click any image above for larger version
All Nippon Airways (ANA) announced a special livery that supports the recovery effort in Japan. Last week, one of their Boeing 767-300ERs (JA611A) showed off the special “Forward together as one, Japan” livery.
On May 2nd, ANA displayed a Boeing 777-300ER (JA786A) with the relief-related message at New York’s John F Kennedy Airport (JFK) for photographers and invited media.
“ANA wishes not only to support those who have been affected by the earthquake, but also move forward together with them to rebuild the region,” ANA spokes person told Airline Reporter. “For our global passengers, ANA would like to reassure our commitment to safety and top quality services through this message as well.”
As of March 13th, all ANA international flights have been operating on their normal schedule. Since April 13th, ANA has been back to flying to all the domestic airports it regularly serves as well as additional relief flights to Senai and Yamagata.
ANA is not sure how long the special livery will fly on the aircraft, but it will be at least through the month of May. NYCAviation has all 13 photos taken by Manny Gonzalez.
This story was a joint effort between AirlineReporter.com and NYCAviation.com